Troubleshooting Common Problems with Single and Dual Zone Beverage Coolers: WIKI Expert Guide
- Share
- Issue Time
- Jul 15,2025
Summary
Discover comprehensive solutions to common problems with single and dual zone beverage coolers. Expert tips from WIKI to help you keep your cooler running perfectly.
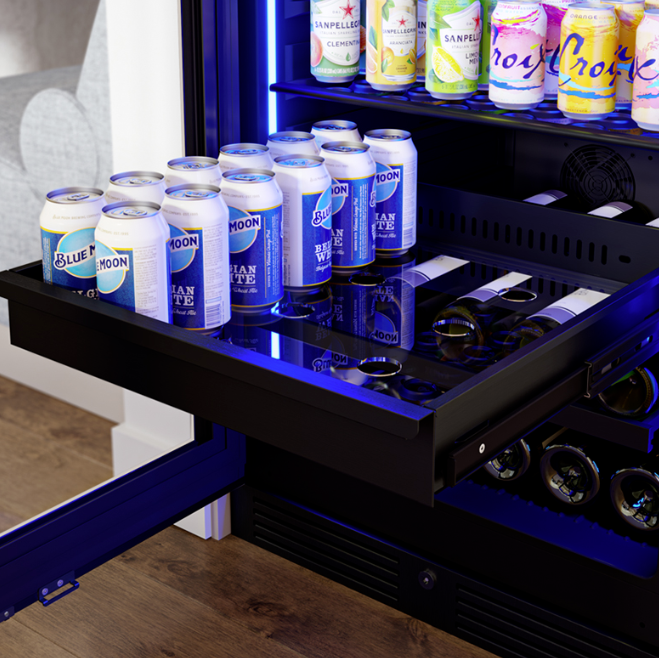
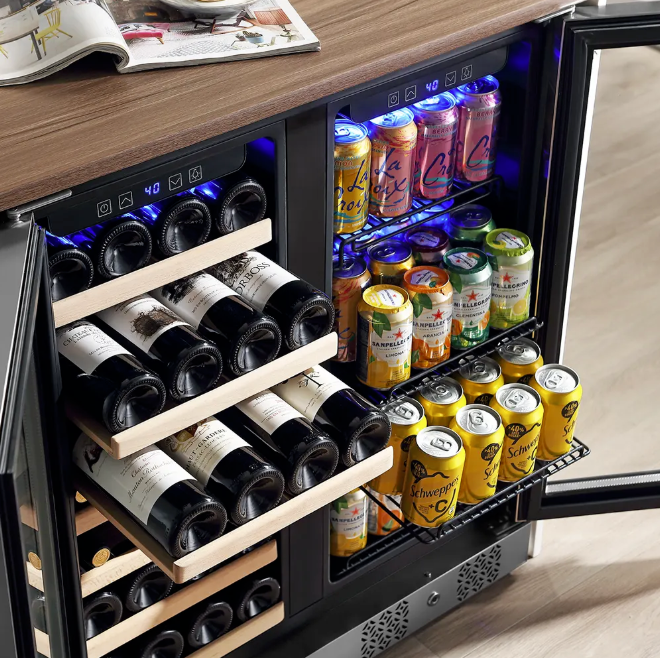
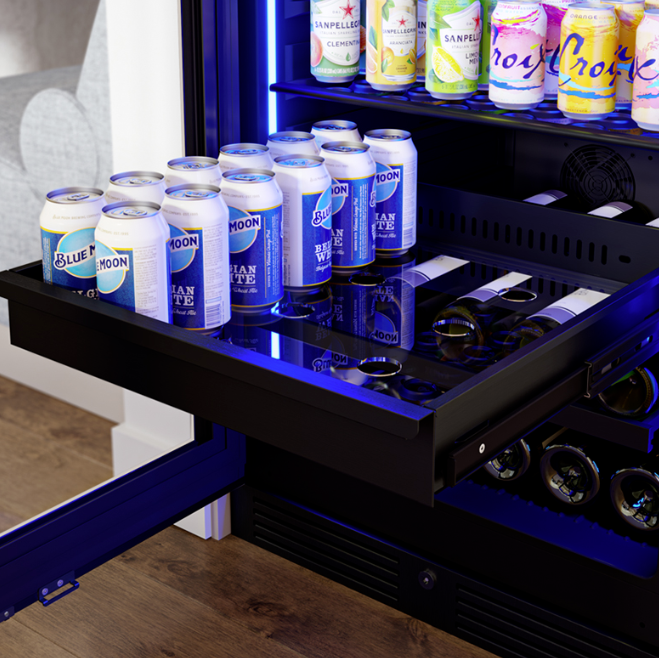
Maintaining optimal performance from single and dual-zone beverage coolers is essential to maintaining the quality and taste of your beverages. Whether you are a commercial establishment or a home hobbyist, knowing how to troubleshoot common problems will ensure your cooler operates efficiently and reliably. In this guide, WIKI provides expert insights to help you diagnose and solve common beverage cooler problems to avoid costly repairs and downtime.
Common Beverage Cooler Problems
Although beverage coolers are designed to be durable, they can still face some problems over time. The most common problems include:
- Inadequate or no cooling
- Fluctuating or inconsistent temperatures
- Excessive noise or vibration
- Ice or frost
- Leaking or dripping
- Display or control panel failure
- Door seal failure
- Electrical or power problems
This guide provides detailed troubleshooting steps, prevention tips, and solutions tailored for WIKI customers for each problem.
Inadequate or No Cooling: Diagnosing and Solving Problems
One of the most frustrating problems is when your beverage cooler doesn't cool properly, or even stops cooling altogether. There are a number of factors that could cause this:
Check power and electrical connections
- Make sure the cooler is securely plugged in.
- Verify that the outlet is working properly by testing it with another appliance.
- Check the power cord for damage or frayed cords.
Check thermostat settings
- Verify that the thermostat is set to the appropriate temperature, which is usually between 38°F and 45°F for beverages.
- Reset the thermostat if necessary and allow the unit to stabilize.
Check condenser coils and ventilation
- Dirty or dusty condenser coils can reduce efficiency. Use a soft brush or vacuum to clean the coils.
- Ensure there is adequate ventilation around the cooler. Clogged vents can affect heat dissipation.
Evaluate the compressor and fan
- Listen to the compressor; it should cycle regularly.
- Check that the fan is running smoothly; a malfunctioning fan can affect cooling.
Investigate refrigerant levels and leaks
- If the cooler still doesn't cool, it may have a refrigerant leak or a low refrigerant charge.
- Contact a professional technician for leak detection and refrigerant refill.
Temperature Fluctuations or Inconsistencies
Maintaining a consistent temperature is essential for properly preserving beverages. A common problem is a faulty thermostat or temperature sensor, which can cause inaccurate readings and uneven cooling. To resolve this issue, inspect the sensor for defects and recalibrate or replace it according to the manufacturer's guidelines.
Poor air circulation inside the refrigerator is another factor that affects temperature stability. Excessive or improperly placed bottles can block vents and restrict airflow. Ensure that bottles are properly spaced and clean indoor fans and vents regularly to promote effective air circulation.
A damaged door seal can also cause unstable temperatures by allowing hot air to enter the refrigerator. Inspect the door seal for cracks, gaps, or signs of wear. If damaged, replace it immediately to maintain a tight seal and optimal internal temperature.
Frequent door openings can cause cold air to escape and warm air to enter, resulting in temperature fluctuations. To avoid this, minimize door openings and consider installing an external temperature display so that you can easily monitor the temperature without entering the room.
Excessive Noise or Vibration: Troubleshooting Tips
Excessive noise or vibration in a beverage cooler often indicates a mechanical problem. Start by checking the compressor and fan—clicking, humming, or buzzing noises may indicate loose parts. Tighten all mounting screws and replace worn or damaged fan parts to restore quiet operation.
Another common cause of vibration is an unlevel unit. Use a level to ensure the cooler is perfectly upright and adjust the leveling feet as needed. Proper leveling not only reduces vibration, but also helps the unit run more efficiently.
Finally, remove the access panel to inspect the internal components. Check for any loose wires or parts that may be causing the noise. Carefully secure any loose components to prevent further interference and ensure safe and quiet operation.
Ice or Frost: Prevention and Solution
Ice buildup inside a beverage cooler can reduce cooling efficiency and even cause leaks. Common causes include: faulty door seals that allow hot, humid air to enter; frequent door openings that cause internal humidity to build up; and a malfunctioning defrost system that fails to prevent frost buildup.
To fix this problem, first turn off the cooler and manually defrost to remove any existing ice. Replace any damaged or worn door seals to maintain a tight seal. Also, check the defrost heater and timer—if either component is faulty, they should be replaced to ensure proper system operation and prevent future ice buildup.
Leaking or Dripping: Diagnosis and Repair
Beverage cooler leaks are often caused by a clogged or frozen defrost drain. When the drain becomes clogged with debris or ice, the water from the defrost cycle has nowhere to go and can overflow into the interior of the unit. To fix this, use a pipe cleaner to clear the drain hole or flush it with warm water to restore proper drainage.
Another common cause of leaks is an overfilled or misplaced drip pan that can easily accumulate condensation. Be sure to empty and clean the drip pan regularly and check that it is properly positioned to catch the water from the defrost cycle. Additionally, high ambient humidity can exacerbate condensation—lowering indoor humidity or improving ventilation can help prevent excess moisture and leaks.
Faulty Display or Control Panel
Electronic control issues can affect the cooler's proper temperature regulation. An easy first step is to reset the control system: unplug the power cord for 10-15 minutes, turn off the cooler, and then restore power. If the control panel has a reset function, use that to restart the system.
Next, check the wiring and connections for any loose or damaged components that could cause the problem. If the problem persists, you may need to replace the faulty control board per the manufacturer's instructions. Also, check for firmware updates that improve system performance and address known issues.
Failed Door Seals and Their Effects
A damaged door seal can significantly reduce cooling efficiency by allowing cold air to escape and warm air to enter. To identify problems, visually inspect the seal for cracks, tears, or gaps. An easy way to check its effectiveness is to perform the dollar bill test—cover the door with a dollar bill and ensure that the resistance is uniform across the seal.
If the seal is damaged, it is critical to replace it promptly. When installing a new seal, carefully follow the manufacturer's instructions to ensure that the seal fits securely, thereby maintaining the cooler's sealed environment and optimal performance.
Electrical and Power-Related Issues
Power problems such as power surges, tripped circuit breakers, or wiring faults can damage the cooler and interrupt its operation. If the circuit breaker is tripped, the first step is to reset the breaker to restore power.
To protect the cooler from future power surges, a surge protector is highly recommended. For ongoing electrical problems, it is best to consult a licensed electrician to ensure safe, proper diagnosis and repair.
Preventive Maintenance for Long-Term Reliability
Regular maintenance extends the life of your WIKI beverage cooler:
- Clean the condenser coils semi-annually.
- Replace the door seals annually or as needed.
- Check and calibrate the thermostat regularly.
- Keep interior and exterior surfaces clean.
- Ensure proper ventilation and avoid overloading.
Conclusion: Ensure Optimal Performance of Your Beverage Cooler
By understanding common issues with single- and dual-zone beverage coolers and applying these detailed troubleshooting steps, you can significantly improve the reliability and efficiency of your equipment. Regular maintenance, close monitoring, and timely detection of problems can avoid costly repairs and ensure that your beverages are always stored at the ideal temperature.
WIKI is an embedded refrigeration appliance manufacturer. We specialize in the development and manufacture of embedded and vertical frost-free refrigeration equipment with a monthly production capacity of 4,500 units. We provide high-performance commercial wine cabinets, beverage cabinets, freezers and other refrigeration products for corporate users. We are committed to providing excellent products and professional support to ensure that your beverage cooling solution will always run perfectly for years to come.
Welcome to contact us to order embedded refrigeration equipment. Trust WIKI to meet all your beverage cooler needs - expert solutions, comprehensive maintenance tips and unparalleled support.
OEM/ODM Customizable 125L Wine & Beverage Cooler Solutions with side by side door - for Global Brands and Distributors
OEM/ODM Customizable Dual Zone Beverage Cooler with Double Glass Door and Stainless Steel Handle for Wholesale
OEM & ODM Customizable 83L Beer Cooler – Tailored Cooling Solutions for Global Brands and Commercial Clients
OEM & ODM Customizable 158L Beer Cooler - Ideal for Both Home and Commercial Use, Maximizing Space and Efficiency